A tablet is a solid pharmaceutical dosage form, consisting of a small quantity of compressed powder. There are several types of tablets on the market, including sublingual, chewable, effervescent, film-coated and enteric-coated. This dosage form is acquired for correct recommended dosage, cleanliness, ease of packaging and transportation and less wastage. To achieve the tablet form, powder needs to be compressed and include the right formulation of excipients
The process of tablet compression is split into four different stages.
1. Filling
The transfer of raw materials into position for tablet compression. The homogenised powder is poured into the machine hopper, either manually or via an automated system, whereby the powder flows into the tablet compression chamber.
2. Metering
The removal of excess powders from the compressing machine. As powder reaches this stage, it passes through the feeder system, which comprises of the feeder housing and feed peddles. The feeder housing feeds the powder from the hopper into the die system, where the feed peddles ensure consistency and accuracy in the amount of powder fed into the die. The exact weight of compressed powder is enforced through the adjustable height of the lower punch. Any excess is scraped from the surface and into the next punch.
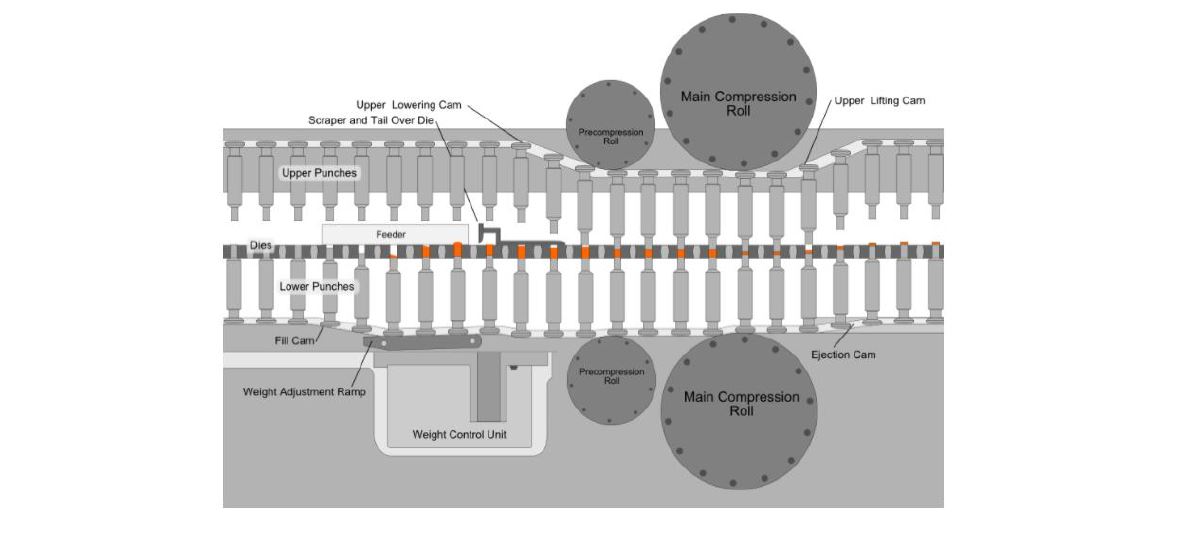
3. Compression
The formation of the tablet, where the upper and lower punches come together under pressure within the die. As the punches move between two large compression rollers, a sufficient amount of force is exerted, where air from between the granules is expelled prior to the commencement of compression. The adjustable height of the punches controls thickness and hardness of the produced tablet.
4. Ejection
The removal of the tablet from the lower punch-die station. The upper punch retracts whilst the lower punch simultaneously rises in the die, pushing the tablet upward to the surface of the die table. The take-off blade deflects the tablets through the discharge chute and into the collection container, usually through a deduster and metal detector.
Tablet compression may appear simple, however it is an intricate process, where many issues can arise. These defects are based on choice of excipient, in-process or machine errors. The most susceptible are due to excipients, where the addition of excipients is inaccurate or errors occurring during the granulation process. Consequently, the product need to be regularly monitored for any variations and maintained to fulfil specifications.
Potential Tablet Defects
Due to Excipient
+ Chipping
+ Friability Variation
+ Mottling
+ Binding
+ Picking & Sticking
Due to Process
+ Capping
+ Lamination
Due to Machine
+ Double Impression
Monitor to prevent defects
+ Weight
+ Thickness
+ Hardness
+ Disintegration
+ Dissolution
+ Lubricants
Author: Jessica Ta – June 2018